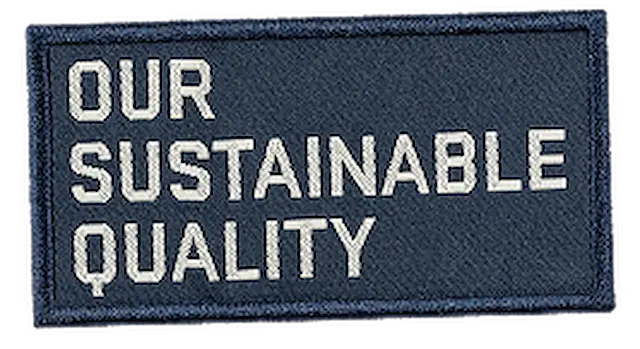
OUR CHALLENGES
We’re proud of the company Blåkläder is – and wants to be– but let’s face it, this is a job that will never be finished. Producing workwear involves many difficult tasks and choices, and there are various challenges we’re working hard to overcome. We’ll tell you all about them here.
FOCUS ON THE FUTURE
CHANGING AN ENTIRE INDUSTRY - WHO CAN DO THAT?
As no textile production is completely sustainable and no sustainability labelling covers the impact of a garment throughout its lifetime – yet – many of us still have some work to do. As buyers, wearers and not least as clothing manufacturers. But who goes first and how? Here are a few tips.
Buyers – ask questions and require that the clothing manufacturer is able to effectively influence sustainability throughout the value chain. Don’t settle for simple declaration models or labelling without verification. Ask if the climate impact can be minimised and how the lifespan can be maximised. This tells you more than the amount of recycled polyester or simplified carbon footprint calculations.
Wearers – choose sustainable production even if it is more expensive and more complicated in the short term. Quality pays off in the long run. And the low-cost culture is really just about passing the buck so workers, communities and the planet bear costs that should really be borne by companies and end-users. Sustainable choices may cost more – but are they really more expensive if they save both the planet and people?
Clothing industry – retain power over key decisions. Don’t delegate things like material sourcing, health and safety and energy use entirely to subcontractors. Not every clothing company is able to own all of its production, but everyone can look at sustainability along the supply chain. It should be done as a matter of course.
CONTROL
SUPPORT MATERIAL SUPPLIERS IN THE SUSTAINABLE TRANSITION
One of our challenges is to get all our material suppliers to switch to more sustainable production. We’ve come a long way, but there are still areas we can influence, and we see it as our responsibility to actively support suppliers in their transition. However, we need to ensure that our partnerships meet our high standards – and when they don’t, we may need to seek new solutions.
Blåkläder works with a limited number of carefully selected material suppliers, many of which we’ve worked with for as long as 15 to 30 years. An obvious advantage of this is that we can develop together and share knowledge. But sustainability work can be both expensive and difficult, and the transition requires major investment, which most businesses can’t afford to do just like that.
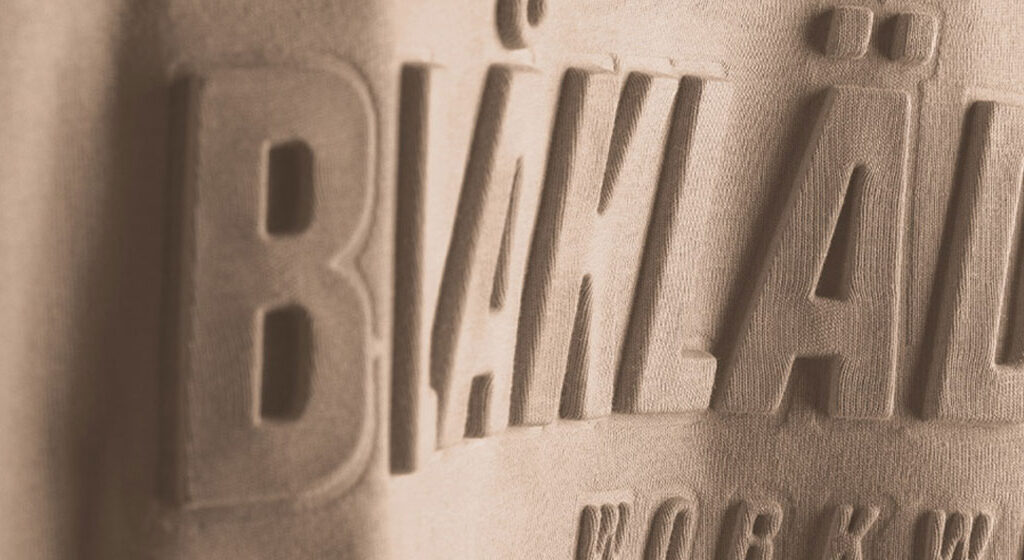
That’s why we want to help more material suppliers step up their sustainability efforts. As an important, loyal customer, we’re often in a good position to require higher standards. We’ve already seen positive changes, although we know we still have a long way to go. This is a factor in the success of our partnerships.
CHEMICALS
PHASING OUT PFAS
Workers in harsh environments – where fire, extreme heat, chemical splashes and oil are commonplace – need extra durable workwear to protect them. Today, the only way to make garments safe enough is often to treat them with chemicals that can be dangerous if they end up in the wrong environment. So we need to strike a balance between benefit and risk.
As of 2025, no new PFAS will be produced in Blåkläder’s value chain.
Chemicals play an important role in making our garments safe, but we don’t want to do any harm to nature or people. When the benefits of a treatment fail to outweigh the risks, we phase out that substance completely, and we’re constantly evaluating how we can keep the use of chemicals to an absolute minimum. This is more difficult when the protection provided by chemicals can’t be achieved in any other way.
PFAS
Fluorocarbons, or PFAS, are chemicals used to give clothing repellent properties that protect the wearer from liquids, oils and grease. However, PFAS have toxic properties and harmful effects on the environment, wildlife and human health. Once applied to a fabric, they can’t be broken down or washed out, which is why they’re also referred to as forever chemicals.
There are already good ways to make clothes water-repellent – but when it comes to protecting against solvents, oils and grease, there are still no good substitutes for today’s chemicals.
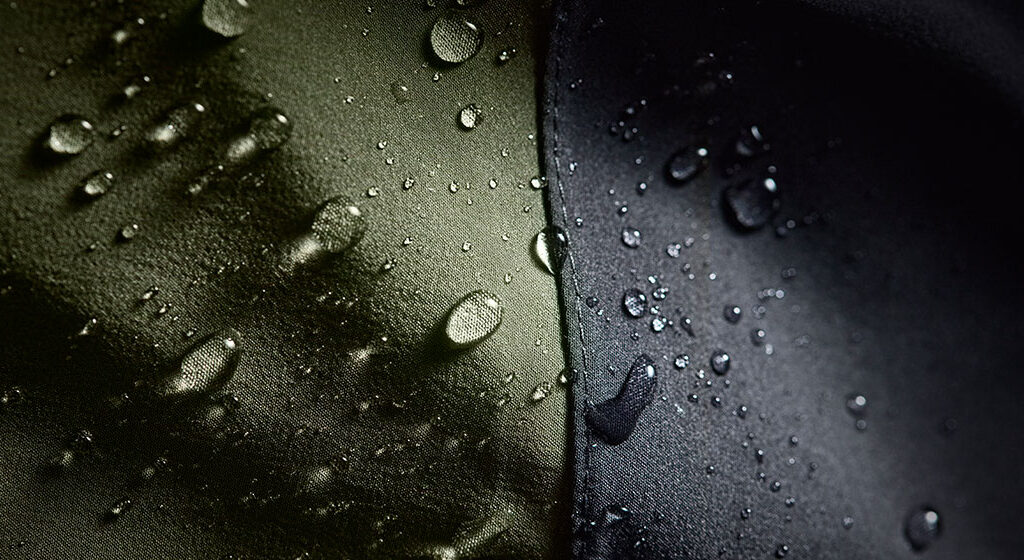
In 2024, we took the important, but complicated, decision to completely phase out PFAS from our production, meaning that no new PFAS will be purchased and put into circulation. Our clothes and fabrics that have already been made with PFAS will be sold until stocks run out.
They’re not harmful to wear and disposing of them would be a huge emission cost, which is the last thing we want.
But what do we do next? Phasing out PFAS in the workwear industry will, for a time, lead to a reduction in both protection and the lifetime of garments. This is not good, but there are lots of us working to find a solution. And it’s the only reasonable way to go.