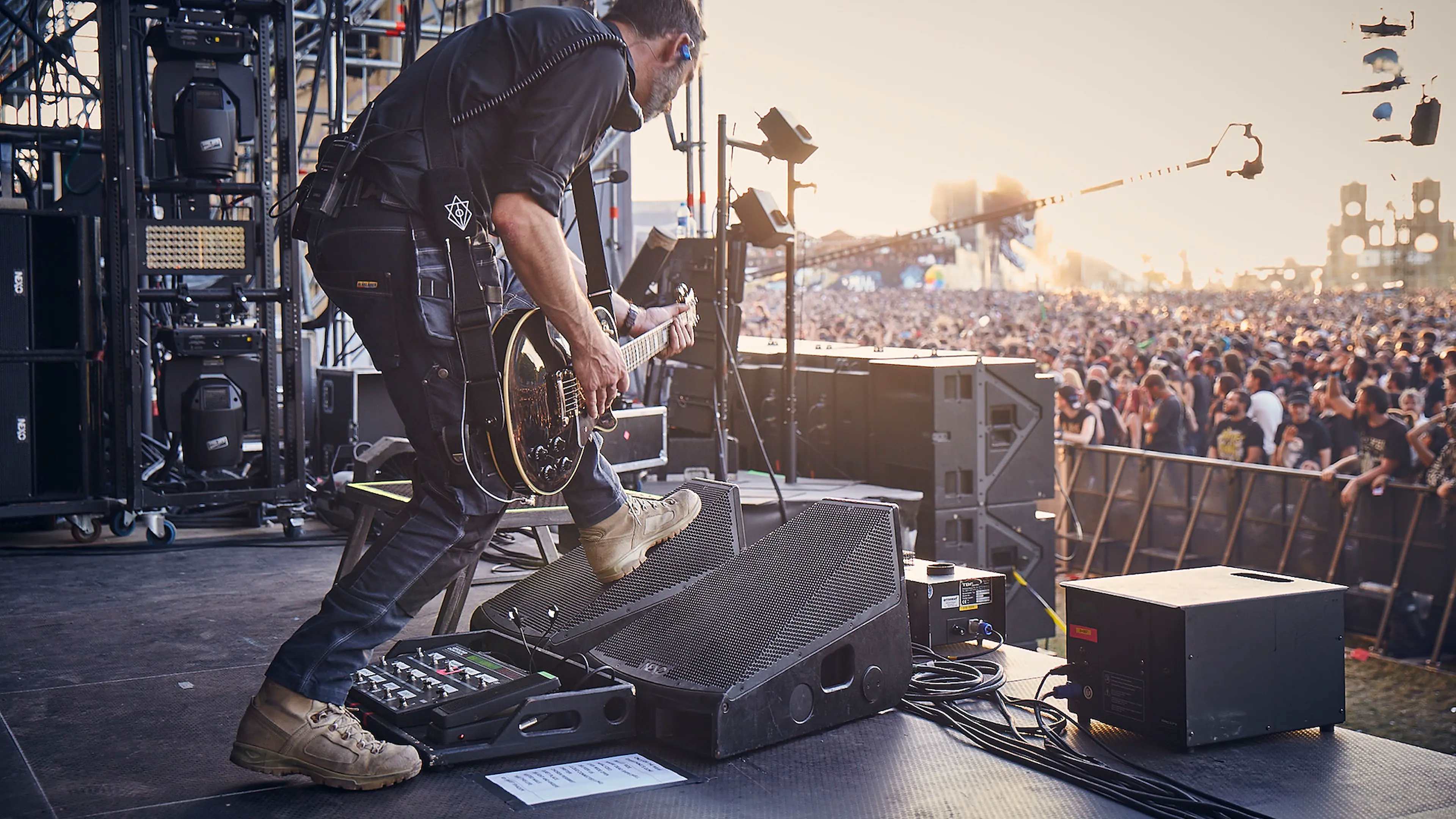

DURABILITY TESTIMONIAL A DECADE ON TOUR IN BLÅKLÄDER
Behind the seams with JesterCrew
While sustainability has become a buzzword in recent years, there are still no more effective way to reduce your environmental impact than reducing consumption. If you can use a product twice as long, you’ve halved its environmental impact. This makes quality even more important, in other words sustainability = sustainability. At Blåkläder we always love a good story where the quality of our products are put to the test. Like when the legendary In Flames roadcrew, also known as JesterCrew, reached out to us for new gear .. after 10 years!
2015 Blåkläder partnered with the legendary road crew of In Flames, known as JesterCrew, providing them with durable workwear for their rigorous and often unpredictable work. Blåkläder also produced the three-part documentary series ‘Build it up, tear it down,’ giving viewers a glimpse of the work that takes place behind the scenes. Now, almost a decade later, Paddi from the JesterCrew reached out to Blåkläder, asking for new gear as the band continues to tour and produce shows globally. We thought it would be the perfect moment to catch up with the crew and reflect on how both their work and Blåkläder’s garments have stood the test of time.
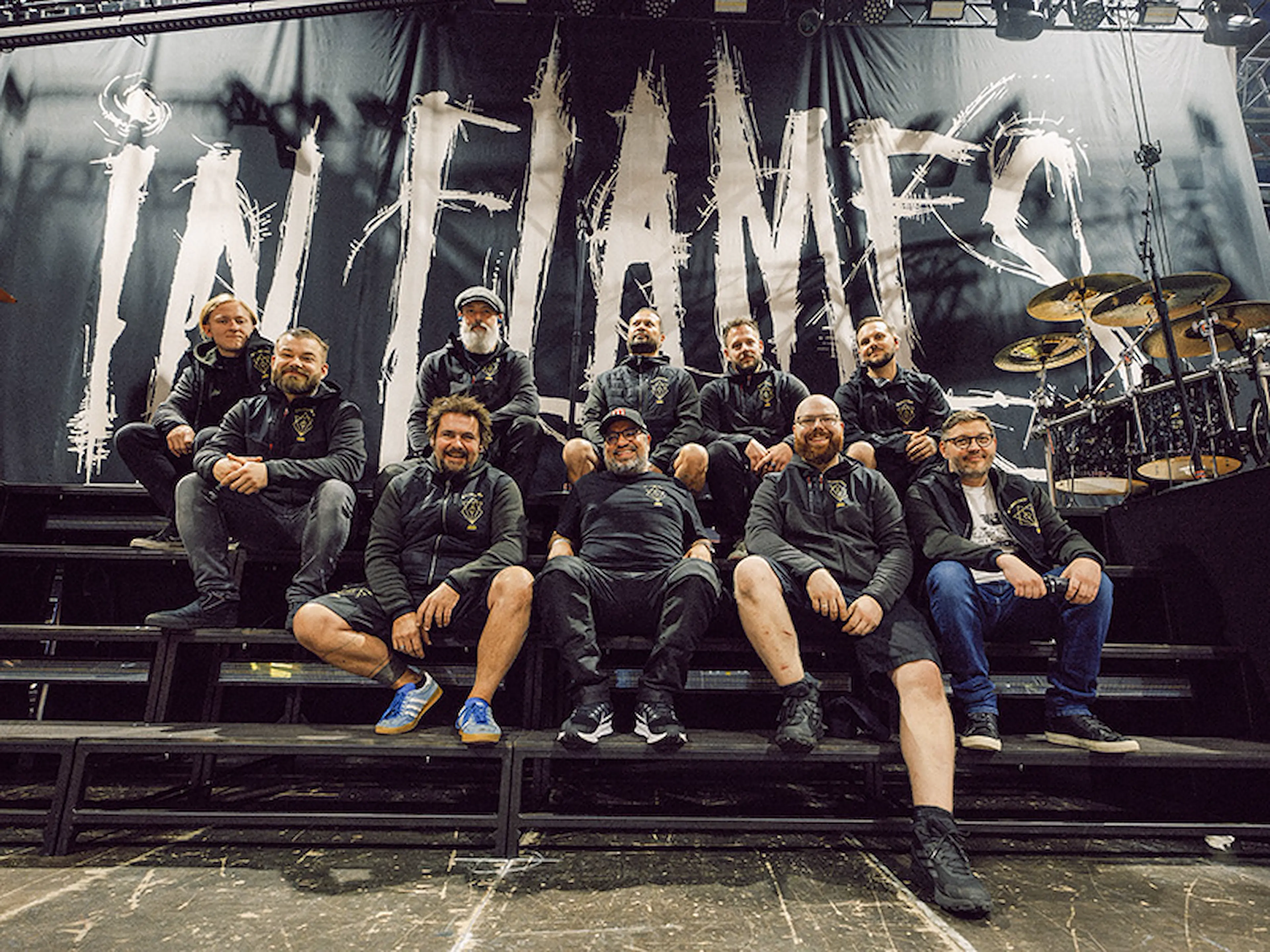
Over the years, JesterCrew has become a tight-knit unit of technicians and production experts. The core team consists of seven people who are always involved, but for bigger productions additional staff might be needed for lighting, sound, drivers, production, and stage management. Greg Winn – guitar technician and stage manager, Patrick ‘Paddi’ Krause – monitor engineer, and Paulo ‘Fish’ Baptista, who is responsible for the band’s guitars, were all part of the crew in 2015 and have worked with In Flames for 45 accumulated years. Despite the high turnover that can come with working in the music industry, many of these team members have stuck around for nearly 30 years.
“Six out of seven of us from 10 years ago are still here,” says Paddi.
The Challenges of Touring
Life on the road comes with its own set of unique challenges, from the physical toll it takes to the constant troubleshooting that’s required to keep shows running smoothly.
“Every day is different,” Greg explains. “One venue may have tricky loading docks, while another might have stringent noise regulations. Then there’s the weather—hot arenas, cold outdoor festivals. It’s a continual balancing act.”
Additionally, the job involves constant travel and grueling hours. Greg estimates that they spend between 150-200 days on the road each year. In the last decade alone, the crew has put on shows in nearly every corner of the globe—Europe, North and South America, Asia, Australia and Africa.
“We’ve probably done over 700 shows,” says Greg, underscoring the relentless nature of their work.
With that extensive experience they all know the importance of good planning to keep the tours running smoothly. “If everything goes according to plan, we can be show-ready in 3-4 hours,” says Paddi. But it’s not always that simple. Even with the best planning, things can still go wrong.
“We once had a show where half the equipment didn’t work,” Paddi recalls with a laugh. “We were sweating bullets, trying everything we could to fix it, and somehow we pulled it off. But those are the days that test your resilience.”
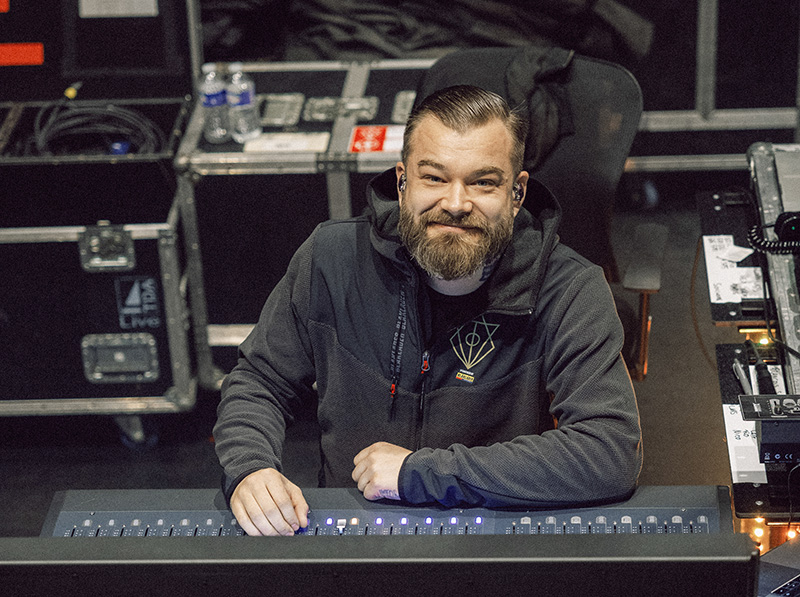
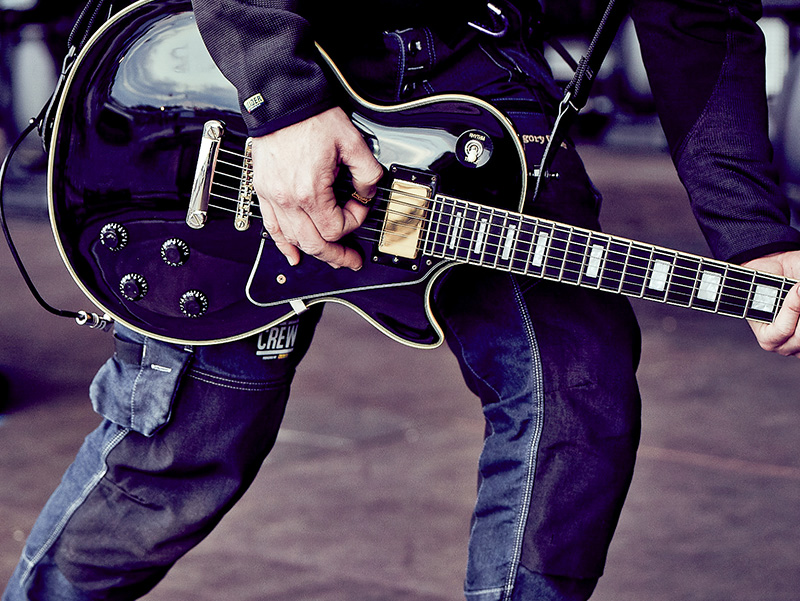
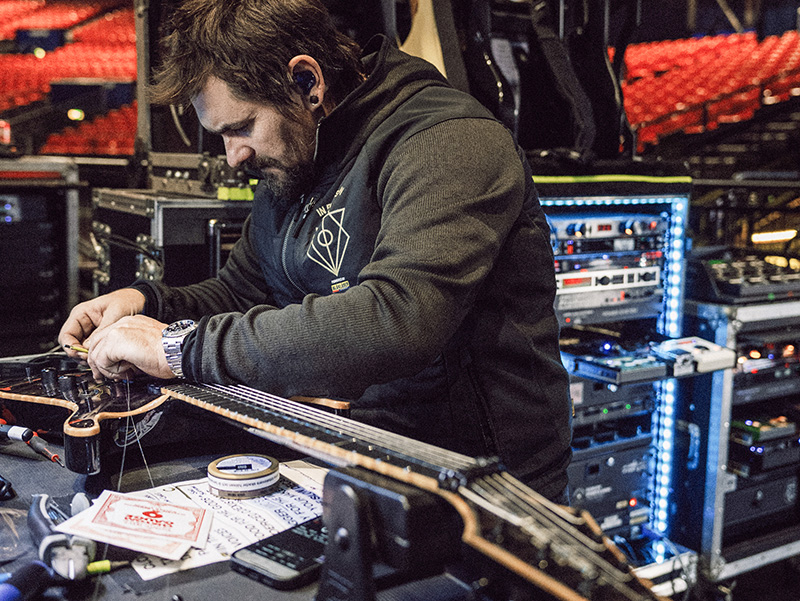
Fish, who is responsible for the band’s guitars, agrees and describes the job as a balancing act between technical and personal challenges.
“Everything has to work perfectly before each show, and if something goes wrong, we have to be able to fix it quickly,” he says.
Despite the pressure, he loves his work and gets an adrenaline rush every time it’s showtime. And the passion for the job is something that clearly shines through in all three of them. The pride of being part of every successful show, seeing the reactions and smiles of the audience, discovering new places and meeting new people as well as the love for the music.
“I’m not a great guitarist myself, but working with guitars gives me incredible satisfaction. Contributing to a successful show gives a feeling that’s hard to beat,” Greg says.

A Tough Job Made Easier with Durable Gear
Among all new challenges and unforeseen situations JesterCrew has faced over the years, one thing has remained constant; their workwear. The members of JesterCrew spend their entire workdays in Blåkläder, and for good reason.
“Regular clothes would never handle the demands of this job,” says Paddi. “I’ve been wearing my Blåkläder pants for ten years, and they’re still holding up.”
For the team, their workwear isn’t just a uniform – it’s a tool that helps them perform their demanding tasks.
“The thing about workwear is that it’s designed for work,” Greg state. “Regular clothes aren’t built to withstand the punishment of touring, and they’re generally less comfortable over time. Workwear prioritizes function, and that’s what we need.”
Fish agrees:
“I like how it becomes part of your routine. You know exactly where everything is in your pockets, which is crucial when time is tight.”
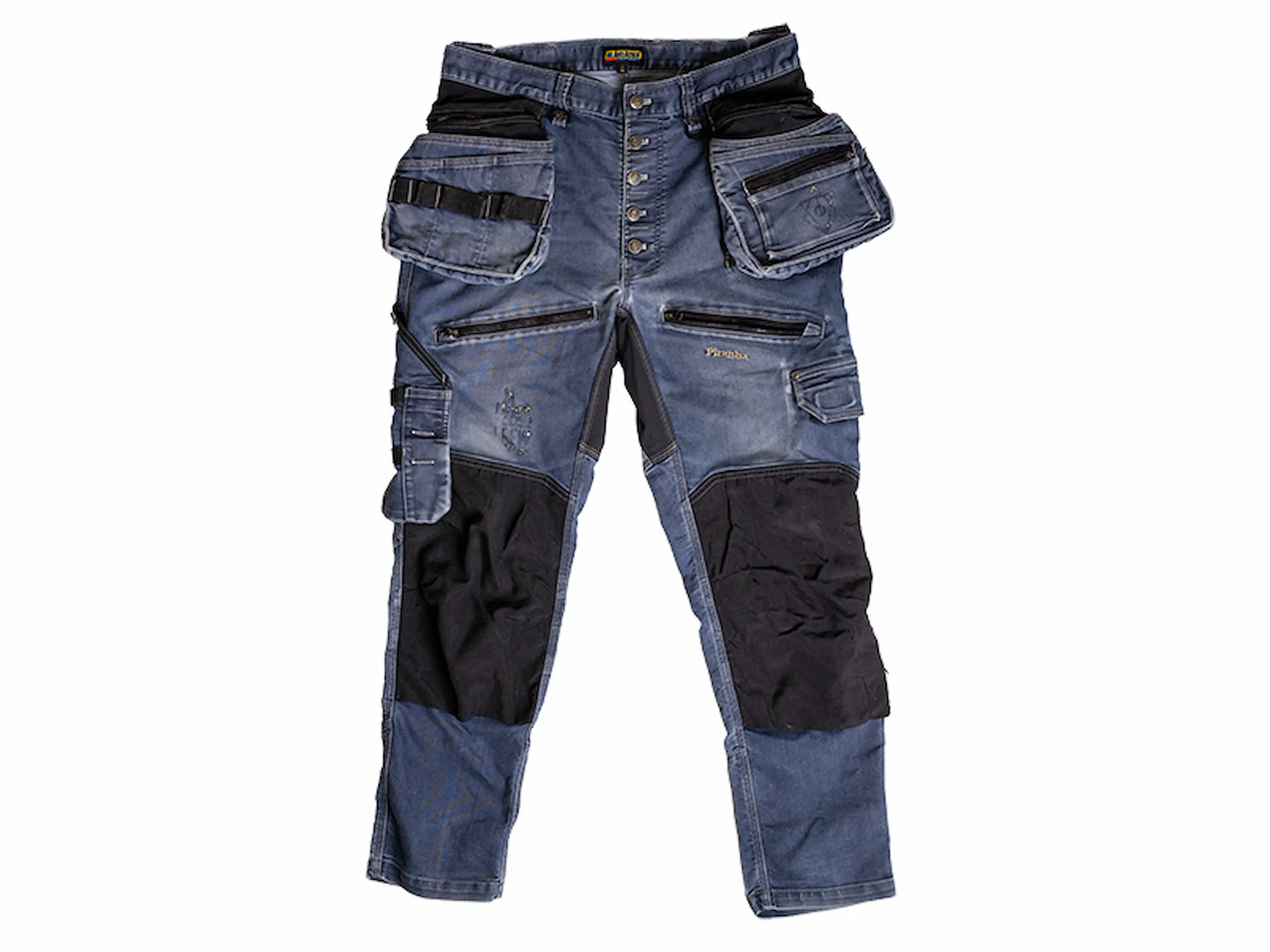
The fact that many of the crew members are still wearing the same Blåkläder garments from 10 years ago speaks volumes about the durability of the clothing.
“There’s some fading, sure,” Greg says, “but no tears, no seams failing. After well over 1,000 days of wear, that’s impressive.”
In an industry where things are constantly changing, it’s reassuring to know that some things, like the durability of a well-made garment, remains the same. Here’s to another decade of hard work, amazing shows, and Blåkläder gear ready for anything.
”We couldn’t be happier. We look forward to another ten years with Blåkläder,” Paddi says.
“There’s some fading, sure, but no tears, no seams failing. After well over 1,000 days of wear, that’s impressive.”
- Greg Winn, guitar technician and stage manager